Imagine this: you’re a blacksmith, hammering away at a glowing piece of red-hot steel. The room is filled with the clang of metal and the scent of burning charcoal. Your creation is almost complete, but you need to make it strong and durable. One last crucial step: quenching, the process that rapidly cools the metal and transforms its properties. But which method should you choose, oil quench or water quench? It’s a question that has plagued metalworkers for centuries, and the answer depends on your desired outcome and the type of steel you’re working with.
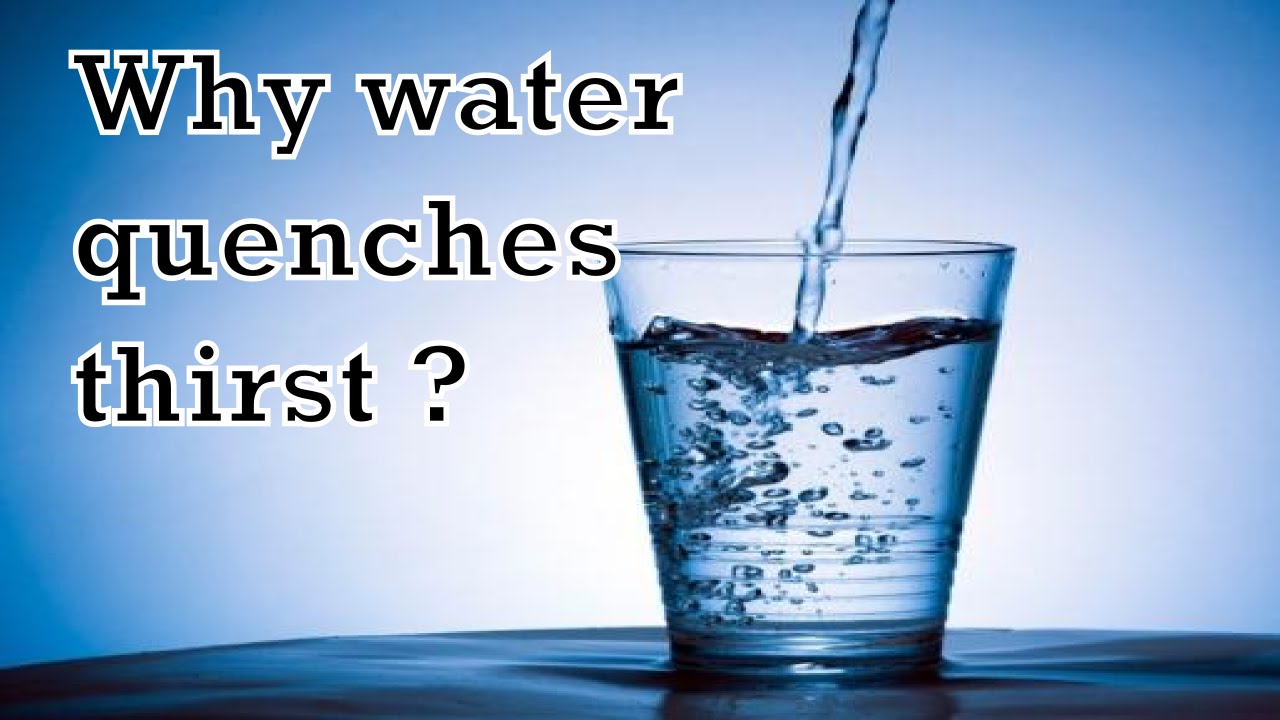
Image: www.youtube.com
Today we embark on a journey into the fascinating world of heat treatment, exploring the key differences between oil quench and water quench, and unveiling the secrets of these powerful techniques that shape the world around us. From the blades of your kitchen knives to the mighty structures of skyscrapers, understanding the power of quenching is essential. So, let’s dive deep into the heat treatment showdown and uncover which method reigns supreme.
The Essence of Quenching: Cooling Down for Strength
Quenching, in simple terms, is the rapid cooling of heated metal to alter its microstructural composition, resulting in a desirable combination of hardness, strength, and ductility. Metal is heated to a high enough temperature to become malleable, allowing for desired shaping, before being plunged into a quenching medium to solidify the new structure. The choice of quenching medium, whether it be oil or water, heavily impacts the final properties of the metal.
Oil Quench: The Gentle Giant
Oil quench, as the name suggests, uses oil as the cooling medium. This method offers a slower cooling rate compared to water quenching, making it ideal for thicker materials or alloys prone to cracking when quenched too rapidly. Oil holds a higher heat capacity than water, meaning it can absorb more heat before its temperature rises significantly. This slower cooling allows for more even heat dissipation, reducing the risk of thermal shock and cracking.
Oil quenching is commonly used for:
- High-carbon steel: It offers excellent hardness and strength, minimizing the risk of warping or cracking.
- Large tools and components: The slower cooling reduces stress and prevents uneven hardening, crucial for large-scale components.
- Tool and die steels: Oil quenching allows for a gradual transition between hardened and softer zones, making the final product more resistant to cracking.
Here are some key advantages of oil quenching:
- Increased toughness: Oil quenching allows for a finer grain structure, improving toughness and impact resistance.
- Reduced warping and distortion: The slower cooling reduces stress and the likelihood of deformities during the quenching process.
- Better dimensional stability: Oil quenching results in less dimensional change, crucial for precision components.
However, oil quenching also has its drawbacks:
- Slower cooling rate: This can lead to a softer product compared to water quenching.
- Risk of oxidation: The oil itself can oxidize the steel, leading to surface imperfections.
- Environmental concerns: Oil quenching requires disposal of used oil, posing potential environmental risks.
Water Quench: The Forceful Plunge
Water quench involves plunging the heated metal into a bath of water. Water, boasting a higher thermal conductivity than oil, enables rapid heat transfer, leading to a much faster cooling rate. This aggressive quenching method is often preferred for thinner materials or when a high degree of hardness is required.
Water quench is commonly used for:
- Low-carbon steel: This type of steel benefits from the rapid cooling, achieving desired hardness without significant distortion.
- Small parts and tools: The fast cooling minimizes the time spent in the quenching process and reduces the risk of warping for smaller components.
- Specific applications: Water quench is often used in applications where a high level of hardness is essential, such as for cutting tools or springs.
The advantages of water quenching are clear:
- Rapid cooling rate: Achieving a high level of hardness in the shortest amount of time.
- Less expensive: Water is readily available and far less costly than oil.
- Suitable for thinner materials: Its quick cooling rate reduces the risk of cracking for thinner pieces.
However, water quenching also presents several challenges:
- Rapid and uneven cooling: This can lead to stress, distortions, and even cracking, especially for thicker materials.
- Increased risk of cracking and warping: The fast cooling can create internal stresses, leading to deformities.
- Greater chance of surface imperfections: Rapid cooling can result in surface roughness or even a hardened surface layer that can be easily damaged.
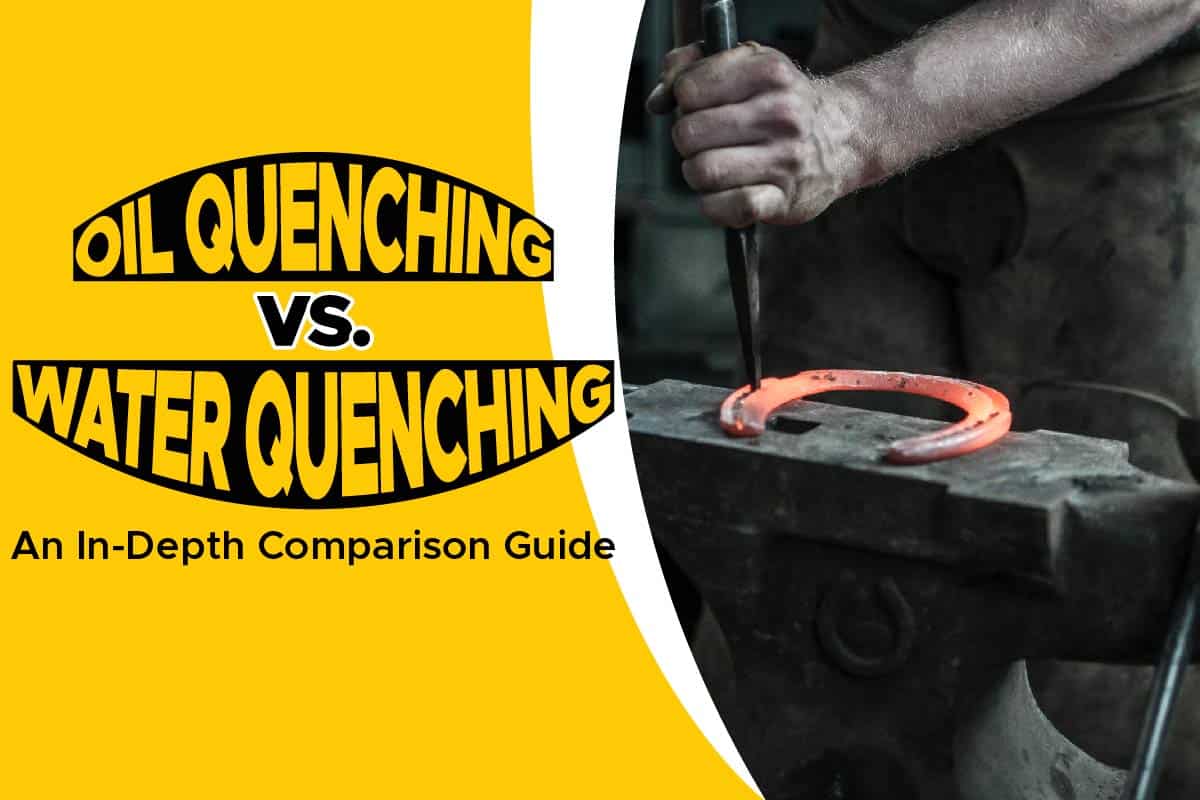
Image: www.mainenewsonline.com
Beyond the Basic: Exploring Variations and Advancements
The world of quenching doesn’t stop at just oil and water. Modern manufacturing embraces a spectrum of advanced quenching methods to ensure precision and optimal results. Here are some popular variations:
- Salt bath quenching: This method utilizes a molten salt bath, offering precise control over the cooling rate and minimizing the risk of distortion.
- Spray quenching: This technique involves spraying a fine mist of water or oil onto the heated metal, enabling localized cooling and fine-tuning of the structural changes.
- Air quenching: This method relies on the natural convection of air for cooling, often used for lower-carbon steels or when slower cooling rates are preferred.
These advanced techniques provide greater flexibility and control over the quenching process, allowing manufacturers to customize the desired properties of their products with precision.
The Expert’s Perspective: Practical Insights for the Everyday
Now that we have explored the fundamentals of oil and water quenching, let’s delve into the real-world insights shared by seasoned metallurgists and heat treatment specialists. Here are some practical takeaways to consider:
- Steel type matters: The choice between oil and water quench is directly influenced by the type of steel being used. High-carbon steels, often favored for their strength, are more susceptible to cracking and require a more gentle quenching process like oil. Lower-carbon steels, known for their ductility, can handle the rapid cooling of water quenching.
- Preheating and tempering: To further control the properties of the steel, preheating and tempering are often employed alongside quenching. Preheating prepares the steel for quenching while tempering reduces internal stresses and increases toughness.
- Understanding microstructure: The final properties of the quenched steel depend on the microstructure created during cooling. By understanding the phases and grain structures that form during the quenching process, metalworkers can target specific properties for their applications.
Oil Quench Vs Water Quench
Conclusion: Finding Your Quench
As we conclude our journey through the world of quenching, it’s clear that oil and water are not simply fluids, but powerful tools that shape the world around us. The choice between oil quench and water quench ultimately rests on the desired outcome, the type of steel being used, and the desired balance between hardness, toughness, and dimensional stability. By understanding the fundamentals of these techniques and incorporating the insights shared by experts, you can unlock the potential of metal and craft creations that withstand the test of time. So, explore further, experiment, and embrace the power of quenching!