Imagine a machine capable of stripping away imperfections, uncovering hidden beauty, and revealing the raw essence of materials. This isn’t a scene from a sci-fi movie, but a reality offered by the 40 lb. capacity floor abrasive blast cabinet. This specialized piece of equipment harnesses the power of controlled abrasion, making it an invaluable tool for industries ranging from metal fabrication and restoration to artistic expression and scientific research.

Image: skatblast.com
But what exactly is a floor abrasive blast cabinet, and why should you care? Essentially, it’s a robust, enclosed workspace designed to direct a high-velocity stream of abrasive particles at a target surface. This process, known as abrasive blasting, allows for precise material removal, surface cleaning, and even intricate surface texturing, all within a safe and controlled environment. This article will delve into the intricacies of this remarkable machine, from its foundational principles to its diverse applications, equipping you with a comprehensive understanding of this powerful tool.
Unveiling the Inner Workings: How a 40 lb. Capacity Floor Abrasive Blast Cabinet Functions
At its core, the 40 lb. capacity floor abrasive blast cabinet is a combination of engineering ingenuity and controlled chaos. Let’s break down its fundamental components and their interplay:
1. The Blast Chamber: A Controlled Environment for Precision
The blast chamber serves as the heart of the operation. This enclosed space, typically constructed from durable steel, provides a safe and contained environment for the abrasive blasting process. Its primary role is to direct the blasting media towards the target material and minimize the escape of abrasive particles into the surrounding area.
2. The Abrasive Media: The Tools of Transformation
The 40 lb. capacity refers to the abrasive media holding capacity, a crucial element of the process. This media can range from fine grit aluminum oxide for polishing to coarse silica sand for aggressive material removal. Different types of abrasive media exhibit varying levels of hardness, density, and particle size, allowing for precise control over the surface finishing process.
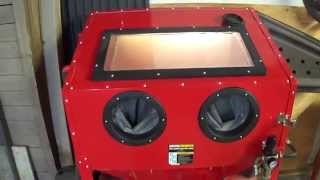
Image: www.resnooze.com
3. The Blast Cabinet’s Powerhouse: The Blast Nozzle
Think of the blast nozzle as the controlled conduit for the abrasive media. It’s a specialized piece of equipment that channels compressed air, directing it at high velocity towards the abrasive media, propelling it towards the target surface. The size and configuration of the blast nozzle directly impact the intensity and focus of the blast, influencing the surface finishing outcome.
4. The Blast Cabinet’s Control System: Precision at Your Fingertips
To ensure optimal and safe operation, the cabinet typically features a control panel with a range of features. These can include pressure gauges for monitoring compressed air supply, flow control valves for adjusting the intensity of the blast, and safety interlocks for preventing accidental operation. This control system is paramount for achieving the desired surface finish while prioritizing operator safety.
The Multifaceted Applications of a 40 lb. Capacity Floor Abrasive Blast Cabinet
The 40 lb. capacity floor abrasive blast cabinet’s versatility makes it an indispensable tool across various industries, transcending the boundaries of traditional surface preparation. Let’s explore some of its key applications:
1. Metal Fabrication and Restoration: Stripping Away the Past, Revealing the Future
In the realm of metal fabrication, abrasive blasting excels at removing surface contaminants, rust, paint, and other coatings. A 40 lb. capacity floor abrasive blast cabinet is ideal for preparing metal components before welding or finishing, ensuring a strong and consistent bond. Furthermore, it can be used for meticulous restoration of antique metal objects, restoring their original beauty while uncovering historical details.
2. Surface Preparation: Creating the Perfect Canvas for Finishing
Before applying finishes like paint, powder coating, or plating, it’s crucial to prepare the surface for optimal adherence. A 40 lb. capacity floor abrasive blast cabinet effectively removes surface imperfections, contaminants, and loose particles, creating a smooth and uniform base that promotes excellent bonding. This ensures a durable and aesthetically pleasing final finish.
3. Artistic Expression: Unleashing Creativity Through Controlled Abrasion
Beyond industrial applications, abrasive blasting has emerged as a powerful tool for artistic expression. Artists can utilize the cabinet to create unique textures, patterns, and effects on various materials, including metal, glass, and wood. This creative use of abrasive blasting opens a world of possibilities for contemporary art and design.
4. Scientific Research: Unlocking the Mysteries of Materials
In scientific research, abrasive blasting often plays a critical role in preparing specimens for microscopic analysis. By carefully removing surface layers, researchers can gain insights into the internal structure and properties of materials, furthering the understanding of material science and engineering.
Beyond the Basics: Advanced Considerations for Optimal Use
While the fundamental principles of abrasive blasting remain consistent, achieving the best results requires a deeper understanding of the nuances and advanced considerations:
1. Balancing Abrasive Media Selection and Surface Finishing Goals
The choice of abrasive media should align with the specific surface finishing goal. Fine grit abrasives are suitable for creating a smooth, polished surface, while coarse grit abrasives are more aggressive for removing stubborn contaminants. Experimentation and careful selection of abrasive media are key to achieving the desired results.
2. Optimizing the Blasting Pressure: Finding the Sweet Spot
The blasting pressure directly influences the intensity of the abrasive blast. Higher pressure results in a more aggressive cleaning action, while lower pressure ensures a gentler approach. Adjusting the pressure based on the material and surface finishing requirements is essential for avoiding damage and achieving desired outcomes.
3. Safety First: Implementing Best Practices for Operator Protection
Operating a 40 lb. capacity floor abrasive blast cabinet requires strict adherence to safety protocols. Always wear appropriate personal protective equipment, including a respirator mask, goggles, gloves, and protective clothing. Proper ventilation and containment of the abrasive blast are crucial for preventing exposure to harmful particles that can cause respiratory problems and skin irritation.
The Future of Abrasive Blasting: Technological Advancements Enhancing Efficiency
The world of abrasive blasting is constantly evolving, with technological advancements driving greater efficiency, safety, and precision. New innovations are emerging in areas like automatic blast cleaning systems, robotic operation, and advanced control systems. These developments promise to further enhance the capabilities of abrasive blasting, expanding its applications and making it even more accessible to a wider range of industries and individuals.
40 Lb. Capacity Floor Abrasive Blast Cabinet
Conclusion: Embracing the Power of Precision
The 40 lb. capacity floor abrasive blast cabinet stands as a testament to the ingenuity of engineering and the power of controlled abrasion. Its versatility, from industrial surface preparation to artistic expression, highlights its remarkable impact on diverse fields. As you delve into the world of abrasive blasting, remember the importance of understanding its principles, considering safety protocols, and embracing the potential for innovation that this remarkable tool offers. This comprehensive overview of the 40 lb. capacity floor abrasive blast cabinet empowers you to unlock its potential and embark on your own journey of precision and transformation.